**Title: The Role of Diesel Generators in Shock Testing: An In-Depth Analysis**
**Introduction**
In the realm of product testing and validation, shock testing is an essential procedure that ensures durability and reliability in various industries, including aerospace, automotive, electronics, and military applications. The critical nature of shock testing necessitates the use of robust and reliable power sources to simulate real-world conditions effectively. Diesel generators have emerged as a preferred choice for providing the necessary power during these tests, owing to their reliability, efficiency, and resilience. This article delves into the intricacies of diesel generators and their pivotal role in shock testing, exploring their operational mechanisms, advantages, applications, and considerations for optimal use.
**1. Understanding Shock Testing**
Shock testing is a process that evaluates how products withstand sudden impacts or shocks. These shocks can arise from various sources, such as transportation, operational use, or environmental conditions. The primary goal of shock testing is to identify vulnerabilities in design and materials, ensuring that products meet the required safety and performance standards.
Different methods of shock testing exist, including:
- **Drop Testing**: Products are dropped from predetermined heights to assess their impact resistance.
- **Shock Machine Testing**: Specialized machines create controlled shock waves to simulate impacts.
- ** https://www.lkpowerplant.com/product/quick-delivery-emergency-standby-power-400kw-silent-type-diesel-generator-set-for-peru/ **: Products are subjected to extreme conditions, including temperature variations and vibrations.
Each of these methods requires a consistent and reliable power source to operate testing equipment efficiently.
**2. The Functionality of Diesel Generators**
Diesel generators convert diesel fuel into electrical energy through an internal combustion engine. They consist of two main components: the engine and the generator (alternator). The engine burns diesel fuel to create mechanical energy, which is then converted into electrical energy by the generator. This process is known as the diesel cycle, characterized by its efficiency and capability to provide sustained power output.
**2.1 Key Components of Diesel Generators**
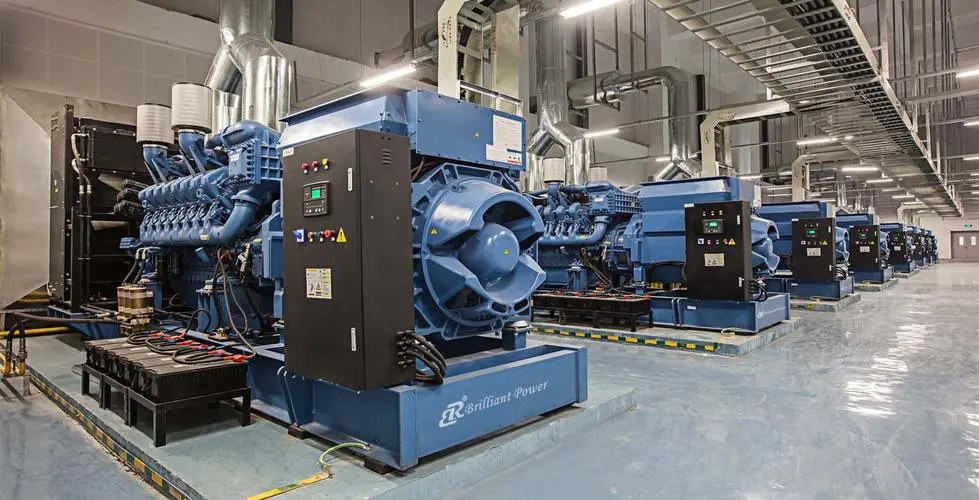
- **Engine**: The heart of the generator, responsible for converting fuel into mechanical energy.
- **Alternator**: Converts mechanical energy into electrical energy, producing AC or DC power.
- **Fuel System**: Manages the storage, supply, and injection of diesel fuel.
- **Cooling System**: Maintains optimal operating temperatures to prevent overheating.
- **Control Panel**: Monitors and controls operational parameters, including voltage, frequency, and load.
**2.2 Operational Mechanism**
When the diesel generator is activated, the engine ignites the diesel fuel, creating combustion that drives the pistons. This mechanical movement turns the alternator, generating electricity. The control panel regulates the output, ensuring that the generator operates within safe parameters. Diesel generators can run continuously for extended periods, making them ideal for long-duration testing scenarios.
**3. Advantages of Diesel Generators for Shock Testing**
Diesel generators offer numerous advantages that make them suitable for shock testing applications:
**3.1 Reliability**
One of the most significant benefits of diesel generators is their reliability. They are engineered to perform under heavy loads, making them ideal for powering shock testing equipment that requires consistent and stable energy output. Their robust design allows them to withstand various environmental conditions, ensuring uninterrupted operation during critical testing phases.
**3.2 Fuel Efficiency**
Diesel generators are known for their fuel efficiency, providing more kilowatt-hours per gallon of fuel compared to gasoline generators. This efficiency translates to lower operational costs, especially during extended testing sessions. The ability to run for long hours without frequent refueling is crucial in shock testing, where time is often of the essence.
**3.3 High Power Output**
Diesel generators can produce significant power, making them suitable for large-scale shock testing setups. They can easily handle the high electrical demands of multiple testing machines and equipment, ensuring that all systems operate smoothly without interruptions.
**3.4 Durability and Longevity**
Designed for heavy-duty applications, diesel generators typically have a longer lifespan than their gasoline counterparts. Their robust construction and ability to operate in challenging environments make them a reliable choice for industries that require long-term testing solutions.
**4. Applications of Diesel Generators in Shock Testing**
Diesel generators find applications across various industries that rely on shock testing for product validation:
**4.1 Aerospace Industry**
In the aerospace sector, rigorous shock testing is crucial to ensure the integrity of components and systems used in aircraft. Diesel generators provide the necessary power for advanced testing equipment, simulating the harsh conditions that aerospace products may encounter during flight and landing.
**4.2 Automotive Industry**
The automotive industry employs shock testing to evaluate vehicle components, such as suspension systems, chassis, and electronic systems. Diesel generators are used to power testing rigs that simulate road conditions, ensuring that vehicles can withstand impacts and vibrations during operation.
**4.3 Military Applications**
Military equipment undergoes extensive shock testing to ensure operational readiness in combat situations. Diesel generators are often used in military testing facilities to power equipment that evaluates the resilience of weapons systems, vehicles, and communication devices against shock and vibration.
**4.4 Electronics and Consumer Products**
In the electronics sector, shock testing is vital to assess the durability of devices such as smartphones, tablets, and other consumer electronics. Diesel generators provide the power needed for testing machines that simulate drops and impacts, ensuring that products can withstand everyday use.
**5. Considerations for Using Diesel Generators in Shock Testing**
While diesel generators offer numerous advantages, several considerations must be taken into account to ensure optimal performance during shock testing:
**5.1 Sizing the Generator**
Selecting the right size of the diesel generator is crucial. The generator must be capable of handling the total load of all testing equipment simultaneously. Proper sizing ensures that the generator operates efficiently and minimizes the risk of overload.
**5.2 Maintenance and Servicing**
Regular maintenance is essential to keep diesel generators running smoothly. This includes routine checks of the engine, fuel system, and electrical components. Proper servicing extends the lifespan of the generator and ensures consistent performance during critical testing operations.
**5.3 Noise and Emission Control**
Diesel generators can produce significant noise and emissions, which may be a concern in certain testing environments. Implementing noise reduction measures and emission control systems can help mitigate these issues, creating a more conducive testing environment.
**5.4 Fuel Quality and Storage**
Using high-quality diesel fuel is essential for optimal performance. Contaminated or low-quality fuel can lead to engine problems and reduced efficiency. Additionally, proper fuel storage practices should be implemented to prevent degradation and contamination.
**6. Future Trends in Diesel Generators for Shock Testing**
As technology advances, the role of diesel generators in shock testing is expected to evolve. Some trends that may shape the future of diesel generators in this field include:
**6.1 Hybrid Systems**
The integration of hybrid systems that combine diesel generators with renewable energy sources, such as solar or wind power, may become more prevalent. These systems can reduce fuel consumption and emissions while providing a reliable power source for testing.
**6.2 Automation and IoT Integration**
The incorporation of automation and Internet of Things (IoT) technology into diesel generators may enhance monitoring and control capabilities. Real-time data collection and analysis can improve efficiency and predict maintenance needs, ensuring optimal performance during shock testing.
**6.3 Enhanced Emission Controls**
With increasing environmental regulations, manufacturers are focusing on developing diesel generators with advanced emission control technologies. These innovations aim to reduce the environmental impact of diesel generators while maintaining their reliability and efficiency.
**7. Conclusion**
Diesel generators play a vital role in the realm of shock testing, providing the reliable and efficient power necessary to simulate real-world conditions. Their advantages, including reliability, fuel efficiency, and high power output, make them an indispensable tool across various industries. As technology continues to evolve, diesel generators will likely adapt and improve, ensuring that they remain a crucial component in the testing and validation of products designed to withstand the rigors of everyday use and extreme conditions. By understanding the operational mechanisms, benefits, and considerations associated with diesel generators, industries can optimize their shock testing processes, leading to safer and more durable products in the market.